Using a
Twin screw barrel for extruder in your plastic squeezer machine can help you get the job done faster and more efficiently. The design of the barrel and the position of the feeding port influence how the screw will feed into the plastic. If you are planning to build your own plastic squeezer, you can learn more about designing the barrel and screws to help you achieve optimum performance.Choosing a suitable screw and barrel is one of the most important considerations in the design of a plastic squeezer machine. These are the two major components of the extruder that will affect the quality of the end product.The most basic and most important variable in screw geometry is the pitch. The pitch is the angle that a helix is shaped. This angle is related to the diameter of the screw. If a screw has too many grooves, then it will not be able to convey material effectively.Another important variable is the length of the compaction zone.The larger the compaction zone, the more work the polymer is subjected to. The size of the compaction zone is proportional to the frictional coefficient at the interface between the barrel and the screw. The length of the compaction zone can vary depending on the type of polymer.
Screw barrel for plastic squeeze machine and drying machine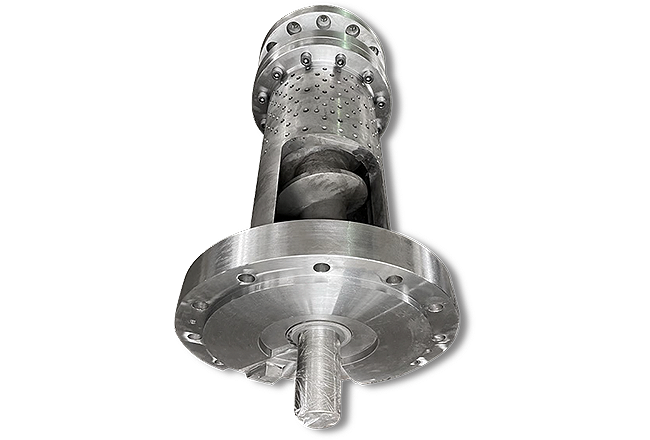
SCREW BARREL for granulation machine/ Pelletizer. We have rich experience in pelleting screw barrel. We have developed a variety of new type of granulation machine/Pelleting screw barrel, with different screw designs, greatly improved the production output, and enhance the service life via continuous practice. The screw barrel can be used for materials like PP, PE, ABS, PET, PA, PMMA and all kinds of engineering plastics. We also water granulation type screw barrel, and design for film with new type high efficiency. The screw barrel adopts the special compulsory feeding design system with high efficiency and output which access to the user's praise.
Developing a comprehensive understanding of the type of wear on screws and barrels in a plastic squeezer machine is critical for maintaining high-quality performance. Excessive wear in these units can have a negative impact on performance, cost, and overall quality. A specialized screw manufacturer can help you develop a maintenance plan that will reduce downtime, energy costs, and improve your bottom line.The most important parameters to consider during screw design are its geometry, its bulk properties, and its rheological characteristics. These parameters will determine whether or not a particular screw is suitable for a given process.The geometry of a screw is determined by its helix angle. The helix angle is a function of the square pitch of the screw. If a screw is designed to work with a material that is shear sensitive, the helix angle needs to be smaller.Using a barrel with proper manufacturing and handling techniques can help reduce corrosive wear. The best time to implement a corrosive wear prevention strategy is during design and manufacturing. However, it's important to know what causes corrosive wear and how to prevent it before you start a project.
There are several types of corrosive chemicals that can attack metal surfaces. Acids are the most common. These chemicals have pH levels lower than seven, and must be handled with caution. The more acidic or alkaline a substance is, the more effective it is as a corrosive agent.The most obvious corrosive agent is hydrochloric acid. The corrosion of this chemical can be extremely destructive to equipment and facilities.Depending on the type of material processed, there are certain factors that affect the quality of the molded part. These factors include the materials used for the front end of the plastics processing unit, as well as the type of screw barrel and barrel linings. These components affect the economics of operation and the overall quality of the molded product.One of the most common causes of abrasive wear in barrels is the presence of foreign particles, which are pushed through the barrel by the rotating screw. These particles may be glass fibers, titanium dioxide pigments, or powdered metals. These particles are typically found in the transition area of the barrel.During feeding of rubber compound in plastic squeezer machine, the shape of feeding port and the position of the opening on the barrel can influence the performance of the feeding process. To improve the feeding structure, a theoretical analysis model can be developed.
This model can help solve actual feeding problems and can also provide a rough quantitative description of the feeding process.In cold-feed extruders, the feeding process is mainly affected by the feed structure. As a result, the rubber compounds are squeezed through the feed-wedge clearance in a nonlinear wedge region. During the process, the rubber strip is dragged by the rotating screw flight.X2F is a breakthrough in plastic injection molding technology that melts polymer at a controlled pressure. This new process can be used to mold high filler loadings, metal filled feedstocks, and non-conventional materials. It is also capable of molding lenses with little birefringence.The company claims the machine is easy to operate and costs less than a conventional injection molding machine. The process is also environmentally conscious and enables the production of plastic optics. X2F has experience molding polyphenylene sulfide, polyphthalamide, nylon, PEEK, polyetherimide, polypropylene, and other polyolefins.Unlike traditional machines, the X2F injection molding unit melts polymer at a controlled pressure without the use of pressure generated heat. This allows the barrel design to be more efficient. Moreover, the patented extruder is designed to perform the function with minimal shear. It features a shutoff nozzle to prevent cold slugs from entering the mold cavity.