Choosing the best
screw barrel is not just a matter of finding one that looks good. It is also important to make sure that it is made of the right material for your application.Choosing the best compression ratio of screw barrel is one of the fundamental parameters to process polymeric materials. It impacts the melting rate of plastic and its overall mixing degree during plasticization. There are several approaches to determining the proper depth compression ratio. Generally, a high compression ratio is used for plastics with high condensation viscosity, and a low one for plastics with low condensation viscosity.The best compression ratio depends on the plastic and its application. Some materials have better running properties on a 4:1 compression ratio, while others run better on a 2.5:1 ratio.Typically, each screw segment has a shearing and scraping flight.
Extruder conical twin screw barrel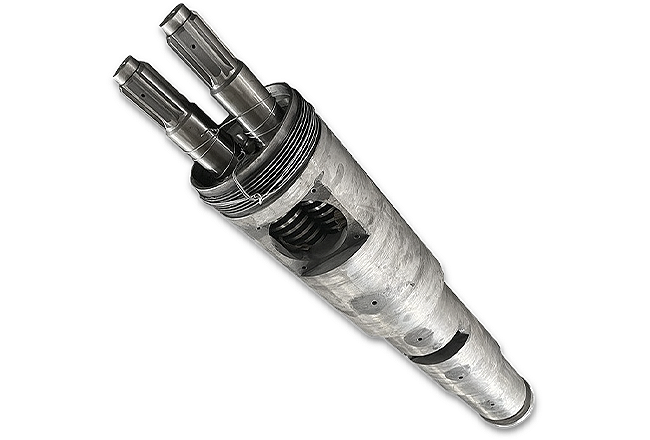
The shearing flight is located near the inner surface of the barrel, whereas the scraping flight is situated near the outer surface. These flights are arranged in alternating sequence around the body. This arrangement is important in the compression and metering section of the screw.The shearing flight has a sharp corner with the leading wall 58 of the thread. This is the most important aspect of the screw because it guides the material to the scraping flight. It also prevents the material from accumulating as a stationary layer on the interior surface of the barrel.Several studies have investigated the effect of flight clearance on screw performance. Some of these studies focused on the metering zone and pressure generating zones of the screw, while others focused on the overall flow characteristics in the screw channel.
The results of these studies have been used to develop new approximations that consider the effects of temperature development, power consumption, and flight clearance. These approximations do not necessarily change the equations describing down-channel flow. However, they do include the effects of flight clearance on the flow characteristics in the screw channel.Often overlooked, the flight face of a screw barrel plays an important role in the polymer extrusion process. Its parameters are important in understanding the performance of your plasticating unit. Using this information, you can choose the best screw design for your application.A typical screw barrel has three zones. The first is a feed zone, where the polymer pellets are fed. The second is a conveying zone, which moves the melt to the die. The last is a mixing zone. The three zones together form the plasticating unit.Among the various problems that can arise in the production process of screw extruders, rapid wear of the screw barrel and screw itself is one of the most important.
It can cause many production problems, increasing maintenance costs and shortening the service life of the screw barrel.There are three different types of wear that can occur in the screw barrel. These are adhesive wear, abrasive wear, and corrosive wear.Adhesive wear occurs when two metals rub against each other. It is also caused by misalignment. The wear pattern appears as scratches on the tips and flanks of the screw flights.Using special tools, a technician can measure wear on screw barrels. The data can be used to assess wear in relation to performance data. The data can also be used to plan repairs.As a result, the data can be used to determine the most cost-effective time to replace parts. Moreover, monitoring screw barrels can reduce material waste, ensuring consistent output.In addition, monitoring screw and barrel wear can help prevent stress on other machine parts. A routine check can also reduce energy consumption.A good measure of wear on screw barrels is a bore gage. An electronic bore gauge can log the data and provide measurement readouts to a computer. It also can be fitted with extension rods to measure the interior of the barrel.