A typical traditional blow molding machine screw can be divided into three parts: feeding section, plasticizing section and separation section. Look at the name to understand! The supply segment is also called the supply segment. After the plastic is delivered to the screw, this process is done inside the tube as the screw rotates, so the friction between the tube and the screw is used to push the plastic to the front for compression. During this period, the plastic is solid!
Parallel cylindrical screws for PE PP sheet product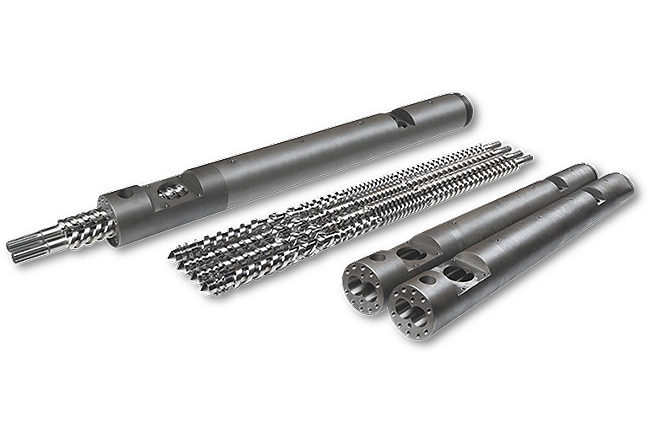
The length of the
screw barrel for plastic squeezer machine material segment is also related to the plastic variety, and the material length varies. This is one of the screw functions of the blow molding machine. Film blowing screw barrel plasticizing section: The purpose of this stage is to press the plastic harder and squash it hard! Dissolve it into a liquid. The plastic moves forward silently from the grade section to the plasticizing section, and is intercepted by the screw, filter, sorting board and machine head to form high pressure. Slowly, gradually, compress further.
At the same time, the raw materials are rotated and mixed by the barrel and the screw. Under the action of shearing and other torture, the flame of the plastic gas soars, the temperature keeps rising, and it turns into a liquid. But at this point part of the plastic body is still solid, and the plastic slowly moves forward to the end of the screw. Due to the effect of frictional heat, the temperature of the end of the screw is very high, and the plastic has become a viscous flow after reaching the end. This is the plasticizing process. It is very important in the screw action of the blow molding machine.
The separation segment has a more general name: the homogenization segment. This is for the plastic to be further plasticized after entering the homogenization section, and then extruded from the screw by static pressure, quantitative, temperature, etc. The separation section is very important in the production process because the discharge rate of the entire melt section determines the production efficiency of the separation section. The discharge speed of the melt section is slow, the separation section will be dragged, and the production speed is slow.