As the cylinder material of the cable machinery
conical screw barrel moves forward, it is heated by the heat generated by the collision and the heat transferred by the cylinder heater. When the temperature exceeds the melting point, the appearance in the cylinder will form a molten film, and the plasticizing section will start from here. It should be pointed out that the starting point of the plasticizing section is generally not the starting point of the compression section. The boundaries of each functional segment depend on the function of the polymer, the shape of the extruder and the operating conditions. Therefore, the boundary line can be changed by changing the operating conditions. However, the geometric section of the screw is determined by the plan and will not change due to changes in operating conditions.
Twin extruder Bimetal screw and barrel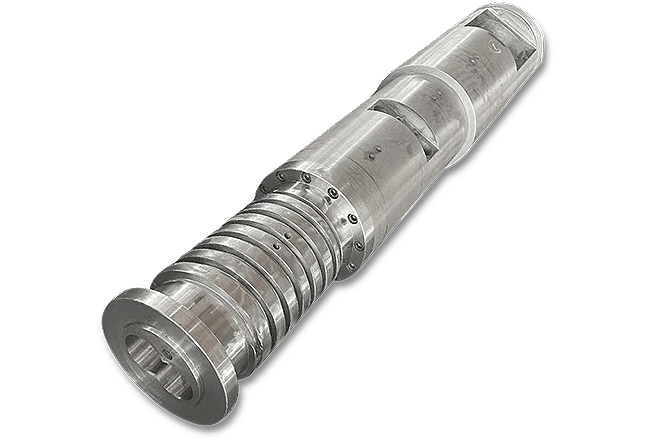
After the material has moved forward, melting will reduce the amount of solid material in all directions. After all the solid polymer disappears, it reaches the end of the plasticizing section, and the melt conveying section begins. In the solids delivery section, the melt is uniformly delivered into the mold. The cylinder of the cable machine screw barrel will have the shape of the mold flow path after the polymer flows into the mold, so when the polymer is released from the mold, its shape is somewhat consistent with the cross-sectional shape of the terminal part of the mold flow path. Since the mold creates resistance to movement, pressure is required to move the material through the mold. This pressure is generally referred to as the die pressure. The die pressure is determined by the shape of the die, especially the flow path, the temperature of the polymer melt, the flow rate through the die, and the rheological properties of the polymer melt.
Die pressure is generated by the die, not by the extruder. The extruder only creates enough pressure to push the material through the die. If the polymerization table, extrusion volume, die head, and die head temperature are all the same, there is no difference between the extruder whether it is a gear pump single-screw extruder or a twin-screw extruder, and the nozzle force is the same. The operation of the cable mechanical screw barrel is actually very simple. Material enters from the hopper. The general material flows from the hopper into the cylinder of the extruder under the action of gravity. Some materials are difficult to move when bored and require special methods to prevent material from splashing onto the hopper. After the material falls on the extruder, it is located in the annular space between the extruder screw and the cylinder, and is surrounded by the automatic thread belly of the thread and the belly thread groove of the butterfly. Jane stopped, and the cicada rod spun. Therefore, the impact force acts on the appearance of the material, cylinder and screw. At least the material is in a solid state, lower than its melting point, and these impact forces act to transport the material forward. Under the action of the cable machinery screw barrel, the granular plastic stored in the hopper continuously works along the screw groove. Under the combined action of the heat applied to the cylinder and the shearing of the screw, the plastic is continuously heated and softened, and then a molten viscous flow state is formed.
At the same time, the melt force at the screw head pushes the screw back. By changing the screw back pressure (return resistance of hydraulic oil), the retreat speed of the screw is adjusted, so as to change the flow condition of the plastic in the screw groove, and then achieve the purpose of controlling the plasticizing performance of the plastic. For example, by increasing the back pressure to improve the degree of homogenization of the melt, at the same time, the temperature of the melt can be increased, which will also affect the conveying capacity of the screw; when the screw retreats, the actual working length changes, causing a decrease in the plasticizing capacity, and at the same time melting The final plastic temperature has a large deviation in the screw axis, and it increases with the increase of the injection stroke and the screw speed. Therefore, using the linear relationship between the back pressure and the melt temperature, the back pressure can be dynamically adjusted according to the actual material temperature to compensate for the axial temperature difference caused by shortening the effective length of the cable machinery screw barrel during pre-forming. Also, by adjusting the back pressure and rotational speed, a large shear force and a low rotational speed are ensured under high back pressure, so that plasticization is uniform at low back pressure and low rotational speed. The moment of inertia is small.